Non Conformances FAQ
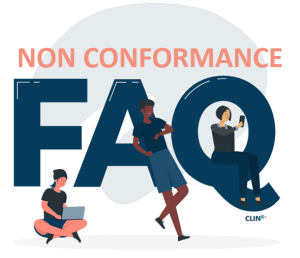
Q: What is a non-conformance (NC)?
A: In the context of the EU MDR, a non-conformance refers to a situation where a medical device, process, or quality management system does not meet the requirements outlined in the regulation (ISO 13485) and the organization’s aligned procedures. Non-conformances can occur during various stages of the medical device lifecycle, including design, manufacturing, post-market surveillance, or quality management. Because of the dynamic nature of technology evolving and standards keeping pace with these changes, non-conformances are part of the QMS need for monitoring and actioning continuous improvement initiatives meet the evolving state-of-the-art (SoTA). It is best for manufacturers to adapt a mindset that NC is not a failure but is evidence that your QMS is effective and once NC has been addressed (CAPA process) it is evidence of keeping up to date with SoTA.
Q: What non-conformances might be found?
A: Examples of non-conformances related to EU MDR include design, manufacturing, labelling, and packaging, post-market surveillance, documentation, and quality management system non-conformances. It could indicate a lack of evidence (clinical data or design validations) or QMS process not being followed or not being effective.
Q: What is CAPA?
A: CAPA stands for Corrective Action (CA) and Preventive Action (PA). It’s a systematic approach used by organizations to identify, investigate, and address issues or non-conformities within their processes, products, or services. The goal of CAPA is to both correct problems that have occurred and implement measures to prevent them from happening again in the future.
Q: What methodology can be used for non-conformance?
A: The Six Sigma methodology, particularly the DMAIC (Define, Measure, Analyse, Improve, Control) approach, can effectively address non-conformances. It involves defining the problem, measuring performance, analysing data to identify the root cause, implementing solutions for improvement, and putting measures in place to sustain the improvement over time.
Q: How can root cause analysis be managed?
A: Several techniques can be employed for root cause analysis, including the 5 Whys technique, Fishbone Diagram (Ishikawa or Cause and Effect Diagram), Fault Tree Analysis, and Failure Mode and Effects Analysis (FMEA). These techniques help in systematically identifying and addressing the root causes of non-conformances, enhancing processes, reducing risks, and improving overall quality and compliance. Bow-tie diagrams are also used to outline causal relationships and potential risk control measures. This is especially helpful to bridge the gap between device faults and how they relate to harm in health hazards assessm.
Q: Why are audits important for managing non-conformance reports?
A: Internal and external audits are processes that assess and evaluate an organization’s operations, financial records, processes, and compliance with all applicable standards, laws, and regulations. Internal audits show the ongoing identification of areas needing improvement (focussed on assessing internal controls and operational processes), while external audits are done by the notified body (NB) primarily focus on product technical document and QMS compliance. Both types of audits ensure the QMS, and its outputs (technical documentation or medical device) keep on conforming to the needs to maintain your QMS certification as a medical device manufacturer and your devices CE mark.
Q: How should non-conformity procedures and processes be set up?
A: Manufacturers should establish non-conformity procedures and processes to guide their teams in implementing best practices for identification, root cause analysis, determination of appropriate changes, ensuring effectiveness and improvement of quality management systems, compliance with ISO standard’s non-conformity requirements, and proper documentation. This systematic approach helps organisations rectify non-conformances, minimize their impact, and work towards a culture of continuous improvement and compliance.