Medical Device Sustainability
What you should consider for your new and legacy device(s)
Sustainability is a pressing matter that medical device developers and manufacturers need to embrace, but it is not straightforward. Moving forward, there is a need to realise that future profitability will be linked to sustainability. From the beginning of the design process manufacturers already take many factors into account, but businesses must now add sustainability factors into this process. This paper looks at where we are now and what does it mean for manufacturers and the design of their medical devices.
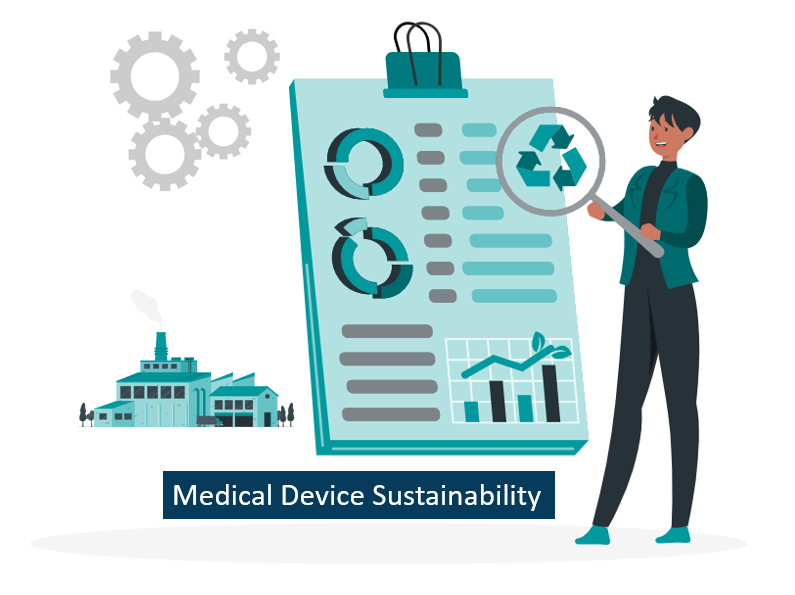
Current MedTech sustainability status and anticipated changes
Globally, health care is responsible for 2·0 gigatons (2 × 109 tons) of carbon dioxide equivalent emissions (CO2e) annually, or 4·4% of global emissions. There are approximately 33,000 medical device manufacturers in Europe with a current value of €140 billion. The UK is the third largest market in Europe (12.1%), with the NHS being the biggest consumer. Using the UK NHS system as a case study, can help give an overview of what may be expected globally in the coming years.
NHS England is one of the largest contributors to greenhouse gas emissions in the UK, responsible for around 4% of the nation’s carbon emissions. As it stands in the NHS medical equipment accounts for 10% of total NHS carbon footprint. This makes the NHS a prime target for Government CO2 reduction goals and actions has been outlined in the ‘Net zero’ plan. In this plan the NHS will be using its considerable purchasing power to drive required reductions in emissions. It is likely they will pursue this in three ways:
- More efficient use of supplies
- Low-carbon substitutions and product innovation
- Decarbonisation of suppliers’ own processes.
Medical device manufacturers must therefore develop their own Net Zero Strategy if they are to be able to continue supplying the NHS, Europe’s third-largest MedTech market.
What does sustainability mean for manufacturers?
When considering medical device sustainability, often people think about carbon footprint and not the whole product lifecycle. Often the end of the lifecycle and whether the device is recyclable, or reusable may be considered. For instance, what are the costs involved, and what are the downstream environmental impacts associated with disposal? Medical device waste is a global problem as devices become more complex and incorporate more electronic components and mixed materials.
However, sustainability also means considering how to reduce carbon emissions, energy and water use, and material waste across its entire lifespan, from design and material selection, to supply chain, to manufacturing and distribution. Sustainable medical devices are better for the environment, attractive to consumers and can provide cost savings, investor attractiveness, and improved brand and competitive advantage.
The industry association MedTech Europe has summarized what constitutes sustainability in medical technology as follows: Good health and well-being, responsible consumption and production, climate action and partnerships are the goals which we see as particularly relevant for our trade association.
Your medical device designers may have already been working to respond to the increasing demand for environmental sustainability from the market while ensuring that safety and usability for healthcare workers and patients is at the top of your priority list.
When it comes to medical devices, sustainability can be achieved at several different levels. Medical devices themselves can be made (more) sustainable in a variety of ways. For example, they can consume less energy, be made using sustainable low-emission production processes and with sustainable materials, lower material use or less packaging, or have longer lifetimes. Each medical device is unique, and there is no “one-size-fits-all” solution to improving sustainability. Decisions made at each stage of the lifecycle impact the long term sustainability of the device.
How can this be done? Strategies that are being widely adopted by companies to achieve net zero include:
- using green energy (switching to a green energy supplier, installing on-site photovoltaic (PV) panel or wind turbine power generation)
- converting to more energy-efficient manufacturing processes
- changing to a lower-carbon or carbon-neutral supply chain
adopting smarter company travel policies (EV company vehicles, remote or hybrid working).
Supply chain impact on medical device materials
The choice of materials has a big impact on the sustainability of a medical device. In a lot of cases, more sustainable materials even improve the device’s tolerability for patients because, for example, fewer harmful substances are used in their production. Sustainability aspects should be incorporated into the device’s design right from the start, so that as few materials as possible are used in production (and those that are used are as well-tolerated as possible), and so that recycling options can be created.
Criteria for sustainable materials include:
- Resource efficiency and low-emission production
- Renewability
- Working conditions for mining, processing, transport, etc.
- Transport routes
- Degradability or reusability
Nevertheless, it is not always possible to use sustainable alternative materials in medical technology. More sustainable alternatives must meet the same criteria as the original product. They must also first be tested, including for biocompatibility, which often involves animal testing.
Sustainable materials must meet the following criteria:
- Stable against mechanical and thermal stresses.
- Easy to clean, disinfect and sterilize.
- Reproducible in terms of production.
- Other properties, depending on the type of use.
If sustainable materials are not safe or their performance is not good enough, they are not a real alternative.
Nevertheless, in many cases, more sustainable options can be found for common, problematic materials. These might be products with an inherently better life cycle assessment and social balance because, for example, they are produced from indigenous plants, or are products that have been mined and transported sustainably or are recycled materials.
However, these materials are often not used for image reasons as much as due to regulatory issues. For a lot of people, having “new” equipment made of solid and tried and tested materials seems more valuable. Alternative materials also have to be researched first and possibly tested for safety and performance, which involves time and costs.
Taking sustainability issues into account in the design stage makes for a challenging process, but the rewards will come both in terms of the environmental impact of your products and ultimately in profit.
- Can you swap petroleum-based plastic for a bio-based material?
- Can you reduce the number of different materials used so that the device is easier to recycle at the end of the lifecycle?
- Can you swap plastic for glass or stainless steel so it can be refurbished and reused?
A material’s carbon footprint also needs to be considered. For example, climate-neutral polycarbonate can be used when designing innovative plastic solutions that are generated by virgin biomass (vegetation) and cooking oils. In some cases, these thermoplastic materials can reuse the tooling previously designed to host standard fossil resins and therefore avoid the need for additional investment.
Device design
Manufacturers need to think about sustainability at the beginning of the design phase and consider the entire lifecycle of the device. Building sustainable medical devices starts at the very beginning, at the design phase. This is where 80% of sustainability decisions are made. These early decisions will have the biggest impact on device sustainability. By taking a more holistic view of medical device sustainability, we can find the opportunities that make the biggest difference with the fewest tradeoffs.
- Which materials are being used?
- Where do they come from (supply chains)?
- Where and how is the device produced?
- How can you best combine safety, performance, and sustainability?
- What happens to the device at the end of its life? Can it be recycled or disposed of in an environmentally friendly way?
- Can you reduce the overall dimensions or weight of the product to minimize materials use, packaging, and distribution-related carbon emissions?
- Can you shrink electronic components to reduce their eventual disposal impact?
- Is there an opportunity to reduce the battery size or switch to a more sustainable battery technology (e.g., rechargeable batteries)?
- Can you use disposable printed batteries, based on non-toxic materials like zinc? (This allows the batteries to be disposed of in regular domestic waste bins, where local regulations allow).
- Can the device be designed to be more durable, minimising the need to repair or replace the device? (By increasing the reliability and modularity, some parts may be reused to support refurbishment or redeployment of those parts to other devices).
Reusable parts are typically components with a longer lifetime and lower failures in time. They are activated when required within the device and, like all the other subsystems, may include a self-test/diagnostic mechanism to flag up a fault in the device.
Lifetime also has a major influence on the sustainability of devices. Longer lifetimes with as few servicing requirements as possible generally result in a more positive life cycle assessment, as fewer devices have to be produced.
Manufacturing process
It’s not just a final product which should aim to be eco-friendly, but the production process should too. Always consider what manufacturing options are open to you, and whether you could reduce energy and water use. Reviewing the manufacturing processes plays an important role in reducing the environmental impact of production.
New manufacturing technology can also help reduce waste, whilst improving productivity and shortening time to market. Having a sound understanding of where energy is used within the design and production of your device is key to reducing the long-term environmental impact of your product.
- Are there manufacturing options that will reduce energy and water use? Strategies to convert to more energy-efficient manufacturing processes. Such as switch to green energy (switching to a green energy supplier, installing on-site photovoltaic (PV) panel or wind turbine power generation).
- Could additive manufacturing be used to reduce material waste?
- Does your contract manufacturer use energy efficient production? Do they follow environmental best practices for carbon capture and disposal of waste streams?
- Can the device be disassembled and reassembled easily?
Products that can be efficiently and economically disassembled and reassembled can be important to minimise the use of glues and welds that can be difficult to remove without damaging parts of the product and that could contaminate other materials in the device. It is also important to ensure the design facilitates both automated assembly and manual disassembly.
How easy is maintenance and repair? While a firmware upgrade can increase device longevity and is a normal part of device maintenance, the lifespan of the medical device can be further extended where a modular design has been used. A modular design can allow easier access to each module, including the battery for testing, repair, replacement or upgrading, as necessary. It also ensures hazardous substances are isolated.
Packaging
EU Directive 94/62/EC in conjunction with Directive 2018/852 demands a significant reduction in packaging waste from 2025. An EU-wide “plastics tax” has been planned for non-recycled materials since 2021.
Medical device manufacturers face several challenges as a result. A lot of devices, such as needles and catheters, have to be packaged sterile, which often produces a lot of waste. The options for substituting or reducing the materials used are often limited due to the sterility requirements.
Other manufacturers can switch to reusable materials or make their packaging as mono-material a possible, which makes it easier to recycle. However, new packaging potentially involving less waste generally also means a design change, which means testing and re-certification by a notified body.
Packaging has huge environmental implications and is an area where most companies are now really trying to cut back. Manufacturers need to ask themselves how packaging waste can be minimized.
- Can recyclable or compostable packaging materials be used?
- Can the packaging form part of the product, or can it be returned for future products?
- Can the use of plastic or petroleum-based foam packaging elements be eliminated?
Distribution
Distribution is important when you are trying to lower your carbon footprint but represents big challenges, especially with exports. Things to consider include:
- Can manufacturing and warehousing locations be chosen to minimize long-distance transportation?
- How much energy consumption does storage and warehousing use?
- Are transport and logistics set up in the most effective way?
- Is the supply chain fully considered?
- Can electric vehicles be used?
Disposal
In a lot of cases, the same sustainable use, disposal, and recycling strategies that are used for other products can also be used for medical devices. How sustainable the disposal or reuse of the device depends on the choice of materials, the production method, and the type of device.
Efforts to reduce the volume of disposable components are constrained by the need to maintain safety standards. The risks associated with hazardous medical waste and biological contamination, as well as the high cost of product sterilisation and reprocessing, have prevented many businesses from moving away from disposable products towards something more sustainable.
However, when it comes to single-use medical devices, for example syringes that are also contaminated with blood or other body fluids, they generally have to be disposed of under special conditions. But even single-use devices can be reprocessed in some situations. Article 17 of the MDR establishes the basic principles for this. It states that individual EU member states must regulate whether or not they permit the reprocessing of single-use medical devices.
It needs to be considered whether more can be done to transition from single-use devices to more reusable devices and/or components, and materials need to be used which can be recycled or degrade naturally.
- Is it possible to switch from a single-use device to a reusable device?
- Can the device or elements of the device be recycled?
- Could it be returned to the manufacturer to be refurbished?
Costs
Some companies would like to implement more sustainability but worry that the safety of their medical devices will suffer and that their costs will increase as a result.
What sustainability can cost:
- The costs of switching to more sustainable processes (research, co-ordination, employing a sustainability manager is worth considering), acquisition of new equipment and software, etc.)
- Higher product and procurement costs.
- Higher production costs, e.g., if production is onshored or methods with lower emissions are used.
But sustainability doesn’t just have costs. In some circumstances, it can help companies increase their revenue.
- Easier to obtain investment and subsidies with fixed sustainability targets.
- Companies can save a lot of money through recycling and reprocessing.
- A reduction in energy and material requirements can also reduce costs.
- Sustainable management makes companies fit for the future.
- Young talent is more likely to choose to work for sustainable companies.
- Sustainability is a winning argument in marketing.
A circular economy has to be the aim if we are serious about sustainability. In a perfect circular economy, there is no waste at all. All resources always flow back into the product cycle.
In the case of medical devices, this can be achieved through reprocessing as well as through recycling. This is particularly important in markets where “new” medical devices are simply too expensive. ISO 17664 provides some guidelines for the processing of medical devices.
Clin-r+ recommendations
The term “sustainability” is often associated with stereotypes – both positive and negative. Regardless of where you stand ideologically, given the increasing scarcity of resources and ever stricter laws, virtually every company will have to get to grips with sustainability in the future. The MedTech sector is no exception.
The regulatory requirements governing safety and performance still have to be followed, particularly in the case of medical devices. Where these two aspects are at risk, environmental sustainability considerations may have to take a back seat. But regulatory requirements cannot be used as an excuse. There are many different ways of being sustainable and it can even help drive innovation.
The elements we’ve outlined above are not the only pathways to medical device sustainability, but they provide a starting point to consider. The result is a medical device that is optimised for sustainability and uses low-power technologies, less hazardous substances and advanced non-toxic battery technology that allows for ecological disposal. Smart and sustainable design also allows for efficient assembly and disassembly to allow repair, refurbishment and reuse of parts, and easy upgrades to firmware and hardware. These elements combine to deliver a medical device with a minimised carbon footprint.
CLIN-r works with medical device manufacturers to address complex questions around sustainability options and their impact on device performance, cost, usability, and manufacturability. We take a holistic approach to help manufacturers make effective decisions and find the fastest and least disruptive route to improved medical device sustainability. Get in touch!
Distribution
Distribution is important when you are trying to lower your carbon footprint but represents big challenges, especially with exports. Things to consider include:
- Can manufacturing and warehousing locations be chosen to minimize long-distance transportation?
- How much energy consumption does storage and warehousing use?
- Are transport and logistics set up in the most effective way?
- Is the supply chain fully considered?
- Can electric vehicles be used?
Clin-r+ recommendations
Risk management documentation and activities need adequate resources. Your device’s safety information should be monitored, evaluated, and resolved quickly.
Clinical evaluation is a crucial part of your technical documentation, so it must be updated routinely.
Post Market Surveillance reports and periodic safety reports must include vigilance information. You need to describe any field safety corrective actions and how they impact your device’s risk-benefit profile.
Technical Documentation should be reviewed regularly and updated whenever a controlled document changes.
You may want to consider outsourcing recurring document updates. Especially given that clinical evaluation and post market surveillance reports need to be updated every 1-5 years. Partnering with an experienced consultancy can be highly beneficial. Consultancies come with specialized resources that can provide extra support where needed and ensure quality work whilst relieving departmental time and effort.
At Clin-r+, we can keep your technical file up to date after you’ve received your CE mark. We offer services in regular updates of literature reviews, clinical evaluation reports, and post market surveillance documentation. Should you have any questions or need professional assistance, CLIN-r+ has a wealth of experience to call upon. Get in touch!
Distribution
Distribution is important when you are trying to lower your carbon footprint but represents big challenges, especially with exports. Things to consider include:
- Can manufacturing and warehousing locations be chosen to minimize long-distance transportation?
- How much energy consumption does storage and warehousing use?
- Are transport and logistics set up in the most effective way?
- Is the supply chain fully considered?
- Can electric vehicles be used?
Clin-r+ recommendations
Risk management documentation and activities need adequate resources. Your device’s safety information should be monitored, evaluated, and resolved quickly.
Clinical evaluation is a crucial part of your technical documentation, so it must be updated routinely.
Post Market Surveillance reports and periodic safety reports must include vigilance information. You need to describe any field safety corrective actions and how they impact your device’s risk-benefit profile.
Technical Documentation should be reviewed regularly and updated whenever a controlled document changes.
You may want to consider outsourcing recurring document updates. Especially given that clinical evaluation and post market surveillance reports need to be updated every 1-5 years. Partnering with an experienced consultancy can be highly beneficial. Consultancies come with specialized resources that can provide extra support where needed and ensure quality work whilst relieving departmental time and effort.
At Clin-r+, we can keep your technical file up to date after you’ve received your CE mark. We offer services in regular updates of literature reviews, clinical evaluation reports, and post market surveillance documentation. Should you have any questions or need professional assistance, CLIN-r+ has a wealth of experience to call upon. Get in touch!